KOMAGE:
Service as a success factor
Service at every stage of cooperation, is one of the KOMAGE success factors: from the detailed consultation on the common process development and execution of press tests, to the fast delivery of replacement and spare parts. Project-based teams from employees of our departments take over the planning and order processing to after-sales service. Flat hierarchies ensure fast processing and optimum communication between our experts and decision-makers on the customer side. A significant advantage the customers all over the world appreciate.
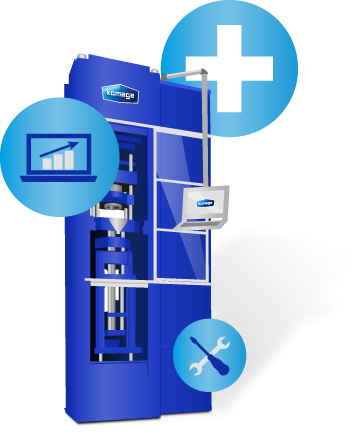
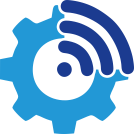
KOMAGE
IIoT
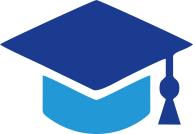
KOMAGE
Academy
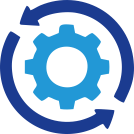
KOMAGE
Factory4U
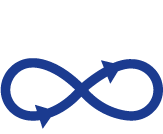
KOMAGE
maintenance service
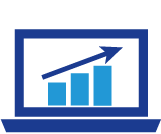
KOMAGE
remote maintenance (Internet)
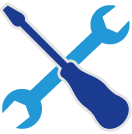
KOMAGE
repair service
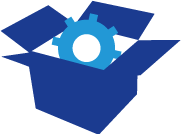
KOMAGE
spare parts service
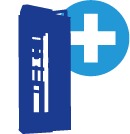
KOMAGE
upgrade service
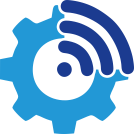
KOMAGE
IIoT - Industrial Internet of Things
The Industrial Internet of Things (IIoT) plays a central role in the modern manufacturing industry. The IIoT technology offered by Komage enables you to optimize your operations, increase efficiency and gain competitive advantages. By connecting our/their machines, sensors and data analysis, they can use real-time information to make informed decisions and improve their production.
The IIoT offers the opportunity to identify bottlenecks, optimize maintenance and minimize downtime. It is a powerful tool that supports companies in being agile and successful in an increasingly digitized world.
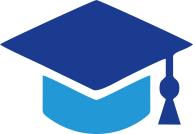
KOMAGE
Academy
Welcome to the Komage Academy - our training centre that offers you and your team the opportunity to continuously develop your skills and get the most out of our technologies. The Komage Academy is a central part of our mission to provide you not only with high quality Press systems, but also with the know-how to optimise your production processes. We are convinced that continuous learning is the key to success.
A deep understanding of the science behind compaction, as well as how to use and maintain the equipment at the customer site, will increase ROI, product quality and reduce downtime. It will also enable customers to take on new challenges and adapt more quickly to the demanding changes they face every day.
The KOMAGE Academy has been developed to be delivered in a customized way. There is a structured course plan, presented with levels and aimed at different skill levels within the organizations, or the customer can choose from a range of topics, which can vary from basic knowledge of compaction technology, to fast setup solutions or advanced energy saving concepts, and design a solution that fits their needs.
The Main topics proposed are the following:
- Compacting Technology
- Filling process
- Programming
- Automation solutions
- Maintenance
- Energy saving concepts
- IIoT
Depending on the topic, the training can be carried out online, at the customer's site or at the KOMAGE Techcenter in Kell am See, Germany. If you require further information or would like to receive a training or seminar offer, please contact our Academy team by email at academy(at)komage.de or call us on +49/6589-91420. Alternatively, you can also get in touch with your KOMAGE contact pers
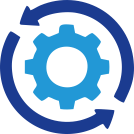
KOMAGE
Factory4U
With Factory4U we offer you a comprehensive range of tailor-made manufacturing solutions to meet your individual contract manufacturing requirements. We have state-of-the-art production facilities, experienced specialists and extensive know-how to manufacture high-quality products for a wide variety of industries.
Our competent team works closely with you to understand your production goals and to offer the best possible manufacturing solution. We offer flexible manufacturing capabilities to meet your part, component or product needs - whether in large or small quantities.
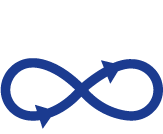
KOMAGE
maintenance service
We will carry out periodic maintenance of your press systems as part of a competitively priced service contract. You will make the most of our favorable service terms after concluding a customized maintenance contract
Your advantage: Professional maintenance of your systems is a crucial factor in extending lifetime, operating times and product quality.
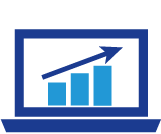
KOMAGE
remote maintenance (Internet)
We will examine your systems using remote maintenance via the Internet as a means of preventive maintenance.
Your advantage: Early identification of potential faults – preventive measures can be initiated in good time.
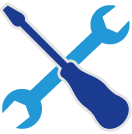
KOMAGE
repair service
Members of KOMAGE´s technical team equipped with the most advanced technical tools will resolve problems on site.
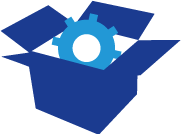
KOMAGE
spare parts service
A team of long-serving employees will support you with spare parts advice, prepare individual quotes and implement short delivery times.
Your advantage: Fast delivery of spare parts from our extensive spare parts warehouse will sustainably increase the process times of your machines. You will receive factory-tested original parts individually optimized to your systems. As we produce most of the spare parts in-house at KOMAGE, they are available as long as your press is in operation.
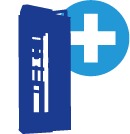
KOMAGE
upgrade service
The KOMAGE Upgrade Service is the solution that will give new life to your KOMAGE Press. Several possibilities are available:
- 1 - Complete mechanical and hydraulic overhaul
Possibility to replace transmission elements, columns, guide elements, guards, bushings and repainting.
- 2- Installation of additional equipment
Depending on the available space, we can design specific solutions to meet the actual needs of the customer, for example a second powder filling system.
- 3 - Upgrade of electrical installation
It is possible to renovate the electrical cabinet according to the latest standards. This is often done in combination with the upgrade of the control system.
- 4 - Upgrade of the control system to the latest standards
The possibility of upgrading the control system of your KOMAGE press will certainly increase its lifetime and availability, as the availability of new components for old control systems cannot be guaranteed after a certain period of time. By upgrading the control system, your press will have the latest standard used by KOMAGE, with the possibility of having remote support from KOMAGE in case of need.
- 5 - Integration of an automation solution
As companies and products are constantly changing, it is possible to redesign or install a new automation solution that meets the actual needs of the customer. KOMAGE offers technical advice to support with the definition of the scope of the Upgrade. Upgraded machines are delivered with warranty. This service is available for all type of KOMAGE presses, from mechanic to electric.