KOMAGE:
For all industries and requirements
With its sophisticated, flexible pressing technology and an extensive service program, KOMAGE serves a wide range of industrial enterprises. Our customers include, among others, global players of the automotive, chemical, pharmaceutical, electrical and aerospace industries who act as pacesetters of technological development in global markets. They make high demands on the precision, process reliability and profitability of their capital equipment. We meet these demands with products and services that are both commercially feasible and deliver high-performance technically.
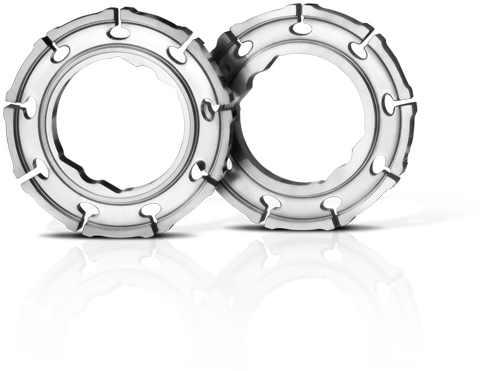
Powder Metal
Industrial Ceramics
Carbon Products
Dental Ceramics
Tungsten Carbides
Ferrite/Magnets/SMCs
Refractory Products
Polymers
Salt
Abrasives
Carbon Brushes
Copper
KOMAGE press systems for powder metallurgy
Powder metallurgy is the largest sector in powder pressing technology. The largest share goes to the automotive industry, which accounts for 70 - 80% of the total capacity. The remainder is divided between mechanical engineering (approx. 15%) and the electrical industry (approx. 5%) and other sectors.
As molded parts for the automotive sector in particular are taking on increasingly complex geometries, KOMAGE with its hydraulic (S Series) and electro-hydrostatic (SE Series) multi-level ejection presses provides the most flexible answer to productivity and quality requirements in the production of these products. Free holding of all pressing axes in the press position is particularly important here as the pressure on the pressing punches can be relieved in both axial directions.
Perfect dimensional accuracy:
KOMAGE press systems for industrial ceramics
Ceramic materials are usually insensitive to high temperatures, have high hardness and appear resistant to chemical substances. Their breaking strength, however, is very low.
Ceramic products are used particularly in wear protection, ballistic protection, and for sealing gaskets in single-lever mixers. In production, high demands are placed on a homogeneous filling, particularly for stepped parts. This is necessary in order to minimize distortion of the products during the subsequent sintering process due to different green part densities. To meet this requirement, KOMAGE supplies powerful, intelligent machines which monitor the pressing process independently, and automatically correct it if necessary.
Depending on the type of production task, a cost-optimized solution can also be achieved by using mechanical presses.
Komage Pressensysteme für Industriekeramik:
Flexible and cost-efficient:
KOMAGE press systems for carbon products
Carbon materials have chemically resistant, thermally stable, self-lubricating properties and are both dimensionally stable and lightweight. These and other properties make carbon attractive for a large number of industrial applications. These products are mainly used for seals in pumps and as friction bearings with excellent reliability due to the existing self-lubricating properties. KOMAGE hydraulic presses enable the cost-efficient production of larger geometric areas with and without stepped cross-sections. Products with smaller geometric areas without stepped cross-sections are produced in large quantities on KOMAGE mechanical-electrical KE presses or also on purely mechanical presses of the K Series.
Komage press systems for carbon products:
Perfect density and dimensional accuracy:
KOMAGE press systems for dental ceramics
Zirconium oxide is not only very hard, resistant to bending and corrosion-resistant but it is also biocompatible and therefore particularly well-suited for use in medical and dental technology. Zirconium oxide is processed as a raw material in powder form and compacted under pressure in a pressing process to form green parts. Homogeneous densities, which are necessary for dental ceramics, can be achieved by means of an isostatic pressing process. The drawback so far: The green part has no exact geometric dimensional accuracy and finish-machining is time-consuming and costly.
The industrial demand for cost-efficient production of green parts made from zirconium oxide led Komage to develop an axial pressing process that achieves both homogeneous density and dimensional accuracy.
We succeeded in doing this: On the new KOMAGE press for dental ceramics, it is now possible to manufacture as many green parts in four hours as with an isostatic press in a week. Our customers receive saleable products in the shortest possible time – without costly refinishing.
Strong in complex shapes:
KOMAGE press systems for tungsten carbides
As particularly wear-resistant materials, tungsten carbides are used in a wide range of industries, such as mining, the construction industry, steel production, metalworking and woodworking. Here, the requirements that are placed on the products differ significantly from each other. Products for mining, the construction industry and steel production do not make very high demands on precision and dimensional accuracy. In the case of products for metalworking and woodworking, however, the requirements for precision and dimensional accuracy are very high. So with carbide cutting tip inserts, for example, the cutting edge may only be a few micrometers.
Our electric (E Series) and electro-hydrostatic (SE Series) presses cover the entire span of standard tungsten carbide products, such as rolls for steel production or cylindrical blanks for tungsten carbide drills and milling tools. Our pressing systems with dedicated automation solutions are in use worldwide for carbide cutting tip production and other high-precision parts.
Komage press systems for tungsten carbides:
Extremely attractive:
KOMAGE press systems for ferrites and magnets
Ferrites and magnets are materials with a continuous attraction for industry. Whether in speakers, parts for voltage transformers in the solar industry, direct-current motors or refrigerators: Produced in their millions, they are an important building block of globalized production. Magnetic materials are also used, however, in specific applications of aerospace and traffic engineering. Our hydraulic presses which are specially equipped with magnetization devices on request are impressive in production due to maximum flexibility, precision and productivity.
We offer powder shaping solutions for applications with and without magnetization for
- Rare earth materials
- Hard ferrites
- Soft ferrites
- Soft magnetic materials - SMC
For long-term results:
KOMAGE press systems for refractory products
Refractory ceramics are used mainly in the iron and steel industry for the manufacture of temperature and wear-resistant parts. Here, high material quality and durability determine the profitability of production. Both full CNC controlled (E-Series, SE-Series and S-Series) and hybrid presses (KE-Series) from KOMAGE meet these special requirements with such things as automatic checking and self-adjusting corrections over the entire press process. The result is quality and cost-optimized production.
One step to the product:
KOMAGE press systems for polymers
Whether in sealing or friction bearing technology or household goods and automobiles – these days polymers are practically indispensable in many industries. KOMAGE press systems take over the production of plastic parts with complicated shapes in huge quantities. Our mechanical – or in some cases also hydraulic – machines compress plastic powder into the desired molded product in a single process with the least possible loss of material.
Special problem solved:
KOMAGE press systems for salt
Industrial salt is an important raw material for the chemical industry and other industries. But to be able to use salt in industrial production contexts, it must first be shaped. The corrosive effect of salt is a particular challenge for automated pressing into geometric and/or dosed forms. KOMAGE took on this challenge and developed an extremely corrosion-resistant system specifically designed for pressing this valuable commodity.
Proven design perfected:
KOMAGE press systems for abrasives
Whether in the metal industry, the automotive industry or in the dental sector: Abrasives or abrasive disks are used practically everywhere in trade and industry. Our press systems can shape grinding disks from a wide range of different materials – from corundum to diamond – and in many different sizes – from 1 to 500 mm. We recommend our tried and tested mechanical or hydraulic press systems for the production of complex shape geometries.
Perfect density and dimensional accuracy:
KOMAGE press systems for manufacturing carbon brushes
The production of carbon brushes with pressing in and cutting off of the copper braids is carried out mainly on our mechanical presses of the K Series. These presses are used worldwide in the production of carbon brushes for the electrical and automotive industries. So the powder presses of the K Series, for example, are the most commonly used standard machines worldwide for the production of carbon brushes. They set new standards in productivity for sliding contacts with an integrated cable scissor unit (press-in and cutting device for cables).
Nowadays, carbon brushes are also manufactured in two-layer technology to prevent spark breakaway edges. This is done on the mechanical presses using a special fill shoe, or on hydraulic presses using two independent filling systems.
Versatile solutions for the electrical industry
Pressed copper parts are indispensable in the electrical industry as they offer excellent conductivity and corrosion resistance. Axial pressing makes it possible to produce these copper components in precise shapes that are optimized for specific applications, ideal for components such as electrical contacts and connectors. This method is particularly efficient and flexible as it allows complex geometries while offering high material utilization, which increases profitability in series production.